Immer wieder kommt es in Unternehmen auf Transportwegen und in deren Umfeld zu gefährlichen Situationen. Die Saint-Gobain Glass Deutschland GmbH setzt nun auf Personenerkennungssysteme, um das Unfallrisiko im Lager zu minimieren.
Nach Angaben der DGUV gab es im Jahr 2018 insgesamt 231.634 Arbeitsunfälle beim innerbetrieblichen Transport. Davon stellten 12.625 Staplerunfälle mit 367 neuen Unfallrenten und fünf Todesfällen einen Schwerpunkt dar. Dabei wurde in 42 Prozent der Fälle das Unfallopfer vom Stapler angefahren, eingequetscht oder überfahren. Bei etwa einem Drittel hingegen verunfallte der Fahrer selbst. Aufgrund schwer überschaubarer Bereiche, Kreuzungs- und Fußgängerverkehr sowie des teilweise schwer einsehbaren Nahbereichs von großen Fahrzeugen und ortsbeweglichen Maschinen ereignen sich auch in der Branche häufig Personen- und Sachschäden.
Personenerkennung im Großglaslager
Die Saint-Gobain Glass Deutschland GmbH hat das Unfallrisiko auf den Verkehrswegen im Lager des rheinländischen Werks Stolberg mithilfe von Transpondersystemen deutlich reduziert und wurde damit als Best-Practice-Beispiel von der VBG ausgezeichnet.
Im Unternehmen wird Floatglas für den Bausektor und die Automobilindustrie produziert. Das Floatglas wird zu sogenannten Bandmaßen im Format 3,21 × 6,00 Meter geschnitten und abgestapelt. Die circa zehn Tonnen wiegenden Flachglaspakete werden von Innenladern oder Vierwegestaplern ins Großglaslager transportiert und zwischengelagert. Aufgrund der Geräuschemissionen der angrenzenden Produktion ist der leise Elektroantrieb der Großfahrzeuge für die sich im Lager bewegenden Personen kaum hörbar.
Kritische Situationen im Lager
Da es in der Vergangenheit auch in anderen Werken innerhalb des Saint-Gobain-Konzerns immer wieder zu unsicheren Situationen wie Beinahe-Zusammenstößen mit Personen oder mit anderen Fahrzeugen kam, wurden die Fahrzeuge mit zusätzlichen Spiegeln und farbigen Spotleuchten ausgestattet. Während die angebrachten Spiegel das Sichtfeld des Fahrers vergrößern, warnen die Spotleuchten Personen im Gefahrenbereich durch den vor dem Fahrzeug auf den Boden projizierten Lichtpunkt. Zusätzlich wurden zur besseren Sichtbarkeit alle Beschäftigten mit Warnschutzkleidung und Schutzhelmen in Warnfarben ausgestattet. Da die Fahrzeuge jedoch sehr groß und unübersichtlich sind und es im Lager viele schwer einsehbare Bereiche an Kreuzungen und zwischen den Lagerplätzen gibt, verblieb ein Restrisiko für Zusammenstöße.
Einführung Transpondersystem
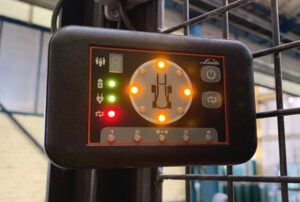
Vor diesem Hintergrund sollte die Sicherheit der Beschäftigten im Lager weiter verbessert werden. Deshalb wurde von der Betriebsleitung der Einsatz eines Transpondersystems (siehe Infokasten auf Seite 5) beschlossen, das sowohl den Fahrzeugführer als auch Beschäftigte im Nahbereich des Fahrzeugs warnt. Dazu wurden die Fahrzeuge und die Beschäftigten im Lager mit einem Sender-Empfänger-System ausgestattet. Auf einem Display im Fahrzeug ist erkennbar, wenn sich eine Person dem Gefahrenbereich nähert, zusätzlich wird ein akustisches Signal ausgelöst. Außerdem wird auf dem Display die Richtung, aus der sich die Person nähert, angezeigt. Die sich im Gefahrenbereich befindende Person wird durch Vibration des Senders und durch ein akustisches Signal gewarnt. Die Signalisierung ist so programmiert, dass diese von der Geschwindigkeit des Fahrzeugs abhängt und so bei höheren Geschwindigkeiten früher alarmiert. Durch diese technische Maßnahme können nun alle Beteiligten rechtzeitig reagieren, indem sie das Fahrzeug stoppen bzw. den Gefahrenbereich sofort verlassen. Insgesamt wurden so vier Transpaletten und drei Vierwegestapler mit dem System ausgestattet.
Zusätzliche Maßnahmen
Das Transpondersystem kann Unfälle nur wirksam verhindern, wenn für die Transportwege geschlossene Bereiche mit Zugangskontrollen ausgewiesen sind. Außerdem müssen jedes Fahrzeug und jeder Beschäftigte im Gefahrenbereich mit einem Sender-Empfänger-System ausgestattet sein. Aus diesem Grund wurde bei Saint-Gobain die Zugangskontrolle im gesamten Produktionsbereich geplant und umgesetzt:
- Analyse vorhandener Zugänge (Zutritte und Notausgänge zum Lagerbereich),
- Schließung nicht benötigter Türen,
- Installation von Schranken an den Zugängen und elektrische Absicherung von Türen,
- Vorhalten von Schließfächern, in denen sich die Ladestationen für die Sender der Beschäftigten befinden,
- Installation einer Zugangskontrolle an allen Eingängen zur Produktion.
Damit wurde auch die Anzahl von Personen im Lager reduziert. Denn Betriebsfremde, wie zum Beispiel Handwerker oder Lkw-Fahrer, können nun nicht mehr den Weg durch das Lager nehmen. Begleitend dazu wurden die Höchstgeschwindigkeiten der Fahrzeuge auf zehn Kilometer je Stunde gedrosselt. Anhand der aktualisierten Gefährdungsbeurteilung wurden die Betriebsanweisungen für den sicheren innerbetrieblichen Transport überarbeitet und alle Beschäftigten unterwiesen.
Die Kombination aus technischen und organisatorischen Schutzmaßnahmen hat zu einer deutlich erhöhten Sicherheit geführt. Die Gefahr von schwerwiegenden Unfällen von Personen im Lager mit Großfahrzeugen wird auf ein geringstmögliches Maß reduziert. Nach einer anfänglichen Eingewöhnungszeit ist der Umgang mit dem System nun vertrauter und die Beschäftigten fühlen sich sicherer.
Fördermöglichkeiten
Für das umfangreiche Schutzmaßnahmenkonzept wurde Saint-Gobain im Rahmen von VBG_NEXT gewürdigt und ausgezeichnet. Ab dem Jahr 2020 wird die Anschaffung von Transpondersystemen auch an Fahrzeugen und ortsbeweglichen Maschinen im innerbetrieblichen Transport im Rahmen des VBG-Prämienverfahrens für Mitgliedsunternehmen aus der Branche Glas und Keramik gefördert.
Die Projektleitung berichtet…
Wie aufwendig war die Einführung des Transpondersystems?
Nachdem wir den Nutzungsbereich des Systems im Lager festgelegt haben und die Infrastrukturkosten klar waren, waren wir uns mit der Geschäftsleitung einig, dass der Zugewinn an Sicherheit für unsere Beschäftigten den Aufwand rechtfertigt. Zudem mussten die Gefährdungsbeurteilung und Betriebsanweisungen aktualisiert und alle Beschäftigten nicht nur in der Funktionsweise des Systems, sondern auch in den Verhaltensregeln unterwiesen werden. Die Beschäftigten waren anfangs skeptisch. Mittlerweile sagen die Fahrer, dass sie sich durch das System sicherer fühlen und Zusammenstöße vermieden werden können. Wir konnten auch die Kollegenschaft, die nicht im Lager arbeitet, und die Beschäftigten von Fremdfirmen wie Zulieferer davon überzeugen, dass die Zutrittsbeschränkungen für das Lager ihrer eigenen Sicherheit dienen.
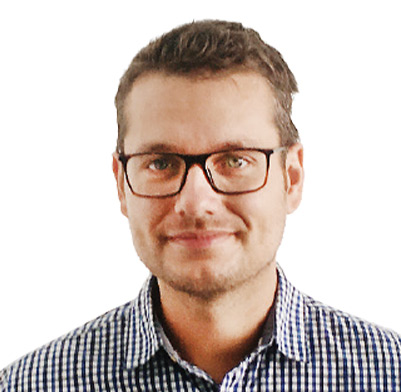